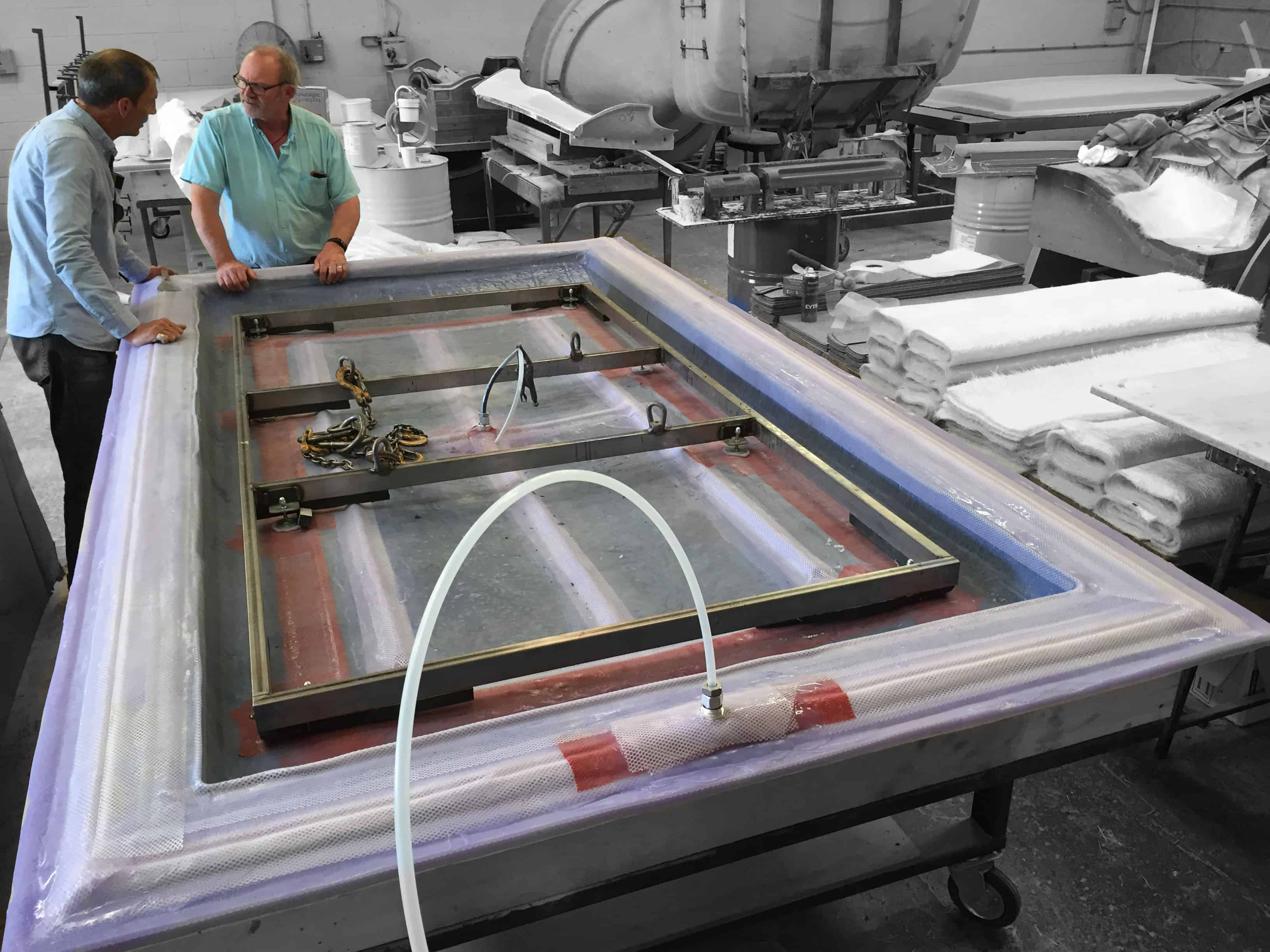
Hereford Glass Fibre Ltd has used Composite Integration technology for several years to complement their manufacturing processes. The company has a wealth of experience in various composites manufacturing techniques, including RTM and VRTM type moulding processes. This allows them to choose the appropriate process for each application.
The production of ‘pop-top’ van roofs for their customer Skyline Roofs Ltd poses some specific challenges. Each moulding has a surface area of 5.2m², with the requirement for an excellent gel coated cosmetic finish on the outer surface.
The moulding has complex PET and cork cores encapsulated within the laminate and uses approximately 20kg of polyester resin.
Currently up to 40 mouldings per week are produced, with the requirement to efficiently increase production volumes as necessary with the minimum of additional investment. The current process achieves a cycle time of 3.2 hours with the individual silicone bags lasting between 275 to 300 cycles.
MD Dillon Muir is enthusiastic about the results achieved using reusable silicone vacuum bags saying;
"By using silicone bags we can improve quality and reduce the mess inherent in the hand-laminating process, as well as reduce the cost that RTM would entail. The silicone bag is also more tolerant of lay-up variations.
We have been using the system for some years, not only for the roofs but with several other projects. We have benefited from the use of silicone bags as, against RTM previously used, we can make very quick changes to the tooling to meet customer requirements in days, not weeks."